In the 1950s, China went through the transition from an agricultural economy to an industrial economy, and now we are going through the transition from an industrial economy to a service economy. Many people do not realize that this is a major transformation of the social and economic structure, so many enterprises feel very painful.
The transition from agriculture to industry
Throughout the history of the development of developed countries, the economic structure has undergone many transformations, from agricultural economy to industrial economy, service economy and experience economy.
Agricultural economics involves growing crops, trees, raising livestock on the land, digging minerals out of the ground, and making simple tools to make farming more efficient. The agricultural economy produces goods that satisfy people’s most basic survival needs. China is one of the birthplaces of the world’s agriculture, which began in the Neolithic Age about 10,000 years ago and has experienced a very long development process.
Industrial economy entered the historical stage with the emergence of steam engine and electricity, people used machines in factories to produce goods in large quantities, and farmers began to enter factories and transform into industrial workers, which was the first large-scale transformation in human history.
Despite attempts to build military and civilian factories during the Westernization movement of the late 19th and early 20th centuries, China’s real industrialization process began with the first five-year Plan from 1953 to 1957. After the completion of the five-year plan, China’s industrial output exceeded agricultural output, which initially laid the foundation for China’s industrialization.
After decades of reform and opening up, China’s industrial economy has developed at an unprecedented speed. In 2010, the added value of China’s manufacturing industry surpassed the United States to become the first manufacturing country. At present, it has 41 industrial categories, 207 industrial middle classes and 666 industrial subclasses, forming an independent and complete modern industrial system. It is the only country in the world with all the industrial categories in the United Nations industrial classification
The transition from manufacturing to service
From the international experience, the turning point of the transition from manufacturing to service is concentrated in the years when the per capita GDP reaches 8,000 to 9,000 US dollars. China’s per capita income exceeded 8,000 US dollars in 2010, and the proportion of people’s spending on manufacturing products reached its peak in 2011, and the per capita income exceeded 9,000 US dollars in 2012.
In 2012, China said goodbye to the peak of industrialization, industrial goods spending continued to decline, service spending grew rapidly, and the growth rate of industrial added value and employment share of the service industry exceeded that of the manufacturing industry, which was the most prominent performance of technology-intensive industries, which reflects the change trend of “manufacturing to service” at the consumption level.
Since then, China has been in the process of economic structure transformation from manufacturing to service, and consumption upgrading is the source of power to promote the transformation of manufacturing to service economic structure, driven by it, the consumer expenditure structure, industrial structure, population flow and urban form changes followed.
The transformation from manufacturing to service has brought the pressure of elimination to traditional concepts and traditional economy, and also brought a huge impact to the previous economy and policies. The entire social and economic system is in a relatively fragile stage, and many enterprises are facing huge challenges.
Taking the construction machinery industry as an example, before 2012, it was an incremental market, and after 2012, it entered the stock market, and the industry experienced years of painful transformation. The reason is that people lack understanding of the characteristics of the service economy, and the traditional concept formed by the agricultural economy for thousands of years is not conducive to the transformation of manufacturing to service.
Mencius said, “Those who work hard govern men, and those who work hard govern men, thinking that intellectual workers rule men, are served by men, and are superior men.” The manual laborer is ruled by others as an inferior person who serves others, and the prejudice against service over millennia has been etched into the depths of the popular psyche.
In ancient times, the basic line of the service industry is collectively referred to as the “lower nine”, the service provider is called the servant, and the occupation of getting paid by serving others is looked down upon, with a “lower” word derogatory name, and “nine” shows its variety, backward traditional concept is one of the main reasons for hindering the transformation from manufacturing to service.
China’s service industry has accounted for more than 50% for ten consecutive years, becoming the largest industry, but many people still despise service, tangible products are still the center of business activities, considered more valuable; Intangible services, on the other hand, are seen as an adjunct to the product and are grossly undervalued
The key to improving service efficiency
From agriculture to industry, large-scale manufacturing has greatly improved production efficiency and made goods more affordable.
However, another difficulty affecting the transformation from manufacturing to service is efficiency. Fragmentation leads to a significant decline in service efficiency compared to manufacturing efficiency (Figure 1). Enterprises still follow the thinking of manufacturing economy and use the idea of increasing scale to engage in services, resulting in high costs and unable to meet customer needs.
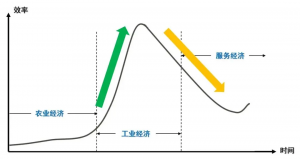
Figure 1: The efficiency of the service economy transition has declined significantly
Based on the experience of developed countries, the service economy is at the higher end of the profit spectrum, which is the famous smile curve in manufacturing (Figure 2).
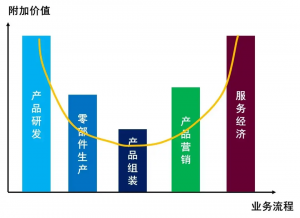
Figure 2: Manufacturing smile curve
However, service is not valued in China, some companies even sell products when the service is free of charge, send high-value services, enterprises can only do trade, the value is not high, customer viscosity is low. On the one hand, it is necessary to educate customers to change their concept of service. On the other hand, enterprises must solve the problem of inefficient service, after all, customers are not obligated to pay for the inefficiency of enterprises.
The solution to the problem of service efficiency lies in technological innovation, the use of knowledge base, artificial intelligence AI, self-service and AR remote support, etc., through the network and platform to improve service efficiency.
If thinking is a wall, the objective world is on the other side of the wall, only solidified thinking can block the pace of enterprise, thinking can not reach the height, the pace can not reach.