In 2024, China’s engineering machinery industry showed signs of recovery after a prolonged downturn. Excavator sales, considered an industry “barometer,” reversed a two-year decline, while domestic sales ended a three-year slump, signaling optimism. Overseas markets remained strong, with several enterprises reporting overseas revenue contributions reaching 50%.
Experts anticipate the industry entering an upward phase of a new cycle. The significant potential in international markets, coupled with the global expansion capabilities of Chinese companies, makes overseas markets a critical focus for domestic brands.
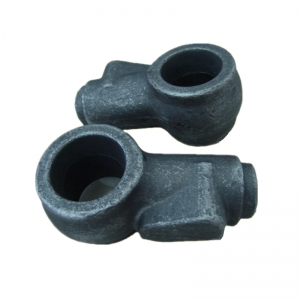
Signs of Recovery
According to the China Construction Machinery Industry Association (CCMA), major excavator manufacturers sold 19,369 units in December 2024, a 16% year-on-year increase. Domestic sales rose by 22.1% to 9,312 units, while exports increased by 10.8% to 10,057 units.
For the full year, excavator sales reached 201,131 units, marking a modest 3.13% growth. Domestic sales increased by 11.7% to 100,543 units, reversing three consecutive years of decline, while exports fell slightly by 4.24% to 100,588 units.
Loader sales also reflected a positive trend, with 108,209 units sold in 2024, up 4.14% year-on-year. While domestic loader sales declined by 3.94% to 54,326 units, exports surged by 13.8% to 53,883 units.
The domestic excavator market’s turnaround was notable. From 2021 to 2023, sales plummeted from 270,000 units to 90,000 units, with declines of 6.32%, 44.6%, and 40.8%, respectively. In 2024, domestic excavator sales rose by 11.7%, reaching 100,543 units. Although volumes remain below the 2021 peak, the growth indicates a recovery in market demand.
A representative from XCMG highlighted signs of stabilization, particularly in earth-moving machinery, which has posted consistent growth in recent months. Policies such as trillion-yuan special government bond projects and large-scale equipment renewal initiatives are expected to further support recovery.
Industry leaders remain confident, citing investment growth, the rising penetration of new energy machinery, and natural equipment replacement demand as driving factors.
Accelerating Global Expansion
China’s engineering machinery enterprises continued to enhance global market capabilities in 2024. Customs data revealed total exports of USD 47.817 billion from January to November, a year-on-year increase of 7.16%. Many enterprises saw overseas revenue contributions rise, with some reaching 50%.
Looking ahead to 2025, companies such as SANY Group and Zoomlion have prioritized international growth. SANY plans to implement a “globalization, digitalization, and decarbonization” strategy, while Zoomlion aims to further develop its localized overseas operations and offer advanced solutions to global clients.
Supportive Policies and Long-Term Growth
Favorable policies continue to boost the sector. The National Development and Reform Commission (NDRC) and the Ministry of Finance recently announced plans to expand large-scale equipment renewal programs in 2025. The initiative is expected to stimulate demand for replacing older machinery, especially those meeting lower emission standards.
Lu Ying, Deputy Secretary-General of CCMA, emphasized the positive impact of such policies, coupled with ongoing industry upgrades in product quality and a shift toward high-end, large-scale equipment. These developments are expected to sustain the recovery and drive long-term growth.
Henan Forging Emperor Industry Co., Ltd. Participates in Alibaba.com’s March New Trade Festival “Hundred Regiments Battle” Event
On February 27th, Henan Forging Emperor Industry Co., Ltd. joined the vibrant “Hundred Regiments Battle” event organized by Alibaba.com as part of their March New Trade Festival. The event, held at the North Aviation Science Park, Building 8, 2nd Floor Meeting Room in Jianxi District, was a dynamic gathering aimed at fostering teamwork, innovation, and business growth.
The March New Trade Festival is a significant annual event by Alibaba.com, designed to boost international trade and provide a platform for businesses to showcase their products and services. This year’s theme, “Challenge Me, Hero,” emphasized the spirit of competition and collaboration, encouraging participants to push their limits and achieve new heights in their respective industries.
The event kicked off at 13:30 with registration and distribution of vests, followed by team-building exercises and ice-breaking activities. Participants were then introduced to the award criteria and prize settings, setting the stage for the day’s competitive spirit. The highlight of the event included the presentation of company flags and headbands, where each company, including Henan Forging Emperor Industry Co., Ltd., showcased their unique corporate culture and team spirit.
The afternoon was filled with motivational speeches, the signing of military orders, and a grand flag ceremony led by the commander-in-chief. The event concluded with a photo session and the distribution of exclusive spring-themed tote bags for participants who shared their experience on social media.
Henan Forging Emperor Industry Co., Ltd. was proud to be part of this inspiring event, which not only provided valuable networking opportunities but also reinforced the company’s commitment to excellence and innovation in the forging industry. The company’s representatives actively participated in all activities, embodying the event’s spirit of teamwork and determination.
As the March New Trade Festival continues to grow, Henan Forging Emperor Industry Co., Ltd. looks forward to leveraging the connections and insights gained from this event to further enhance its global presence and contribute to the thriving international trade community.
Requirements for forging process of flange forgings
Enlarge Font Shrink Font Release
The water inlet and riser of the steel ingot used for flange forgings should be cut off in sufficient quantities to ensure that the forgings have no shrinkage holes or severe segregation. The forging and rolling of flange forgings should determine the corresponding heating specifications according to the material and steel ingot form.
The blank of flange forgings should be pre forged through upsetting process, and the pre forging ratio should not be less than 1.6:1. Flange forgings should be formed by seamless rolling, and the total forging ratio should not be less than 4:1.
The quality grade of flange forgings shall at least comply with Grade II in NB/T 47008-2010.
The heat treatment of flange forgings should be normalizing+tempering to ensure the mechanical properties specified in the product are obtained. During the product manufacturing process, repair welding cannot be used to repair product defects.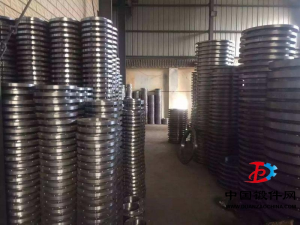
Metallographic testing requirements
Grain size requirement: One piece of each batch of flange forgings should be taken for metallographic testing, and microscopic photographs of X 100 or X 400 should be extracted in the tangential, radial, and Z-directions of the flange; The grain size of flange forgings should be N ≥ 6, and the grain shape and size should be uniform, evaluated according to the method of GB/T 6394. Belt organization requirement: The belt organization of flange forgings shall not exceed level 2, and shall be judged according to the provisions of GB/T 13299. Requirements for non-metallic inclusions in forgings: One piece of each batch of flange forgings should be selected for the evaluation of non-metallic inclusion content, and the evaluation method should follow GB/T 10561.
Mechanical performance requirements
One piece of each batch of flange forgings should be taken for mechanical performance testing.
Ultrasonic testing level requirements: The ultrasonic testing of flange forgings should reach level I of JB/T 4730.3-2005 or level 3 of EN 10228-3:1998.
Magnetic particle testing level requirements
The magnetic particle testing of flange forgings should reach level I of JB/T 4730.4-2005.
The Importance of Rolling Forging
The drag roller forgings are mainly used to support and stabilize the material on the conveyor belt, ensuring a smooth and efficient conveying process. Through high strength and wear resistance, it can withstand the great pressure and friction in the operation of the conveyor belt, extend the service life of the equipment and improve production safety. At the same time, the forging structure is tight, which can reduce the equipment failure caused by wear and ensure the continuity of production. In addition, the drag roller forgings also have excellent corrosion resistance, which can maintain its performance in harsh environments and is not easy to rust or damage. It is often designed with balance and dynamic performance in mind to reduce vibration and noise and provide comfort for the working environment. The roll forging also serves as a guide to ensure that the conveyor belt runs along a predetermined path to avoid deviation or deviation. This helps to improve delivery efficiency and reduce material loss while reducing maintenance costs.
In general, the drag roll forging is an indispensable key component in the conveying system, and its quality and performance directly affect the reliability and efficiency of the entire conveying system. A number of factors need to be considered when selecting a drag roll forgings, including material type, conveying speed, working environment, and the required wear resistance and load carrying capacity. The right choice ensures the stability and durability of the system, reducing failures and downtime. The manufacturing process of the tow roller forgings is also critical. By using advanced forging technology and high-quality materials, denser microstructure and higher mechanical properties can be obtained. These characteristics enable forgings to withstand greater loads and longer service lives. In addition, the maintenance and maintenance of the tow roller forgings is also the key to ensure its long-term stable operation. Regular inspection, cleaning and lubrication can extend the service life of forgings and reduce the occurrence of wear and failure. At the same time, timely replacement of damaged or worn forgings can avoid potential safety risks and production disruptions. To sum up, the drag roller forgings play a vital role in the conveying system. Through the correct selection, manufacturing and maintenance, you can ensure the stability and efficiency of the conveying system, improve production efficiency and quality.
Engineering Machinery Industry Rebounds, Signals Positive Growth
In 2024, China’s engineering machinery industry showed signs of recovery after a prolonged downturn. Excavator sales, considered an industry “barometer,” reversed a two-year decline, while domestic sales ended a three-year slump, signaling optimism. Overseas markets remained strong, with several enterprises reporting overseas revenue contributions reaching 50%.
Experts anticipate the industry entering an upward phase of a new cycle. The significant potential in international markets, coupled with the global expansion capabilities of Chinese companies, makes overseas markets a critical focus for domestic brands.
Signs of Recovery
According to the China Construction Machinery Industry Association (CCMA), major excavator manufacturers sold 19,369 units in December 2024, a 16% year-on-year increase. Domestic sales rose by 22.1% to 9,312 units, while exports increased by 10.8% to 10,057 units.
For the full year, excavator sales reached 201,131 units, marking a modest 3.13% growth. Domestic sales increased by 11.7% to 100,543 units, reversing three consecutive years of decline, while exports fell slightly by 4.24% to 100,588 units.
Loader sales also reflected a positive trend, with 108,209 units sold in 2024, up 4.14% year-on-year. While domestic loader sales declined by 3.94% to 54,326 units, exports surged by 13.8% to 53,883 units.
The domestic excavator market’s turnaround was notable. From 2021 to 2023, sales plummeted from 270,000 units to 90,000 units, with declines of 6.32%, 44.6%, and 40.8%, respectively. In 2024, domestic excavator sales rose by 11.7%, reaching 100,543 units. Although volumes remain below the 2021 peak, the growth indicates a recovery in market demand.
A representative from XCMG highlighted signs of stabilization, particularly in earth-moving machinery, which has posted consistent growth in recent months. Policies such as trillion-yuan special government bond projects and large-scale equipment renewal initiatives are expected to further support recovery.
Industry leaders remain confident, citing investment growth, the rising penetration of new energy machinery, and natural equipment replacement demand as driving factors.
Accelerating Global Expansion
China’s engineering machinery enterprises continued to enhance global market capabilities in 2024. Customs data revealed total exports of USD 47.817 billion from January to November, a year-on-year increase of 7.16%. Many enterprises saw overseas revenue contributions rise, with some reaching 50%.
Looking ahead to 2025, companies such as SANY Group and Zoomlion have prioritized international growth. SANY plans to implement a “globalization, digitalization, and decarbonization” strategy, while Zoomlion aims to further develop its localized overseas operations and offer advanced solutions to global clients.
Supportive Policies and Long-Term Growth
Favorable policies continue to boost the sector. The National Development and Reform Commission (NDRC) and the Ministry of Finance recently announced plans to expand large-scale equipment renewal programs in 2025. The initiative is expected to stimulate demand for replacing older machinery, especially those meeting lower emission standards.
Lu Ying, Deputy Secretary-General of CCMA, emphasized the positive impact of such policies, coupled with ongoing industry upgrades in product quality and a shift toward high-end, large-scale equipment. These developments are expected to sustain the recovery and drive long-term growth.
Current situation and prospects of Russian industrial robots in the world technology market
According to Russian satellite news agency sputniknews, a future that seemed infinitely distant two decades ago has arrived. It is now commonplace to see robots cleaning rooms or factories where hundreds of machines are tended by just a few people. The world robotics market is developing rapidly, so what is Russia’s position?
According to the use of robots, they can be divided into industrial and service categories. Typically, robots on the production floor are industrial robots, while service robots perform the work of providing services to people. For the time being, industrial robots dominate the market: almost 2m have been installed worldwide. But the number of service robots is booming. Industrial robots: Russia is lagging behind
By the end of 2019, there were 5,000 industrial robots in Russia, an average of five robots for every 10,000 workers. The index is still quite poor, 20 times worse than the world average and 160 times worse than Singapore, the world leader. What explains this gap? Mikhail Grigoliev, an entrepreneur in Novosibirsk, believes that the Russian market is not yet ripe for mass robotisation. Mikhail owns a company called Grinik Robotics that makes one-of-a-kind robotic hands for small and medium-sized businesses.
Photo: MIKHAIL GRIGORJEV
Mikhail Gregoriev, general manager of Greenik Robotics
He said:
“Our potential customers don’t want to invest in automation. It is easier for them to hire migrants from nearby countries and pay 20,000-25,000 rubles a month than to spend 1-2 million rubles on a robot complex. Although many people understand that robotic assistants are more efficient and ultimately less expensive than humans. Second, the industrial robot market in Russia is underdeveloped because of the lack of engineers with specialized knowledge and skills.”
Industrial robots are not yet common in Russian companies
In Russia, 95% of the robot complexes are produced abroad, such as fanuc and Kawasaki of Japan, kuka of Germany, abb of Switzerland, and IGM of Austria. There are only a handful of companies in Russia that specialise in industrial robots and few series of products. For now, Russia is lagging behind in homegrown robots and robot “brain” software, but it is booming abroad. About 40% of industrial robots in Russia are used in automobile manufacturing, mainly the classic six-axis manipulator, engaged in welding, car coloring and semi-finished product handling; Another 30% and 15% are engaged in the electronics industry and pharmaceuticals, respectively. The least robotic sectors are shipbuilding, aircraft manufacturing, nuclear power, mineral extraction and agriculture, where the barriers are mainly high prices.
The world’s largest single capacity and largest size impact runner welding manufacturing success
On December 30, the world’s largest single capacity and largest size impact turbine runner was successfully welded and manufactured in Harbin Electric Group, and the world’s first single capacity 500 MW Zhala hydropower station impact turbine generator set runner was born, marking a major breakthrough in the development technology of China’s high head and large capacity impact hydropower unit, walking in the forefront of the world.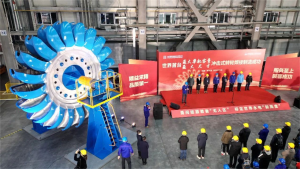
The turbine runner is the “heart” of the hydro-generator set of Zhala Hydropower Station, the backbone power station of the national “storage power transmission”, which provides the source power for the generator to emit 500 MW rated power. Under the unified organization of China Datang Group, the owner of the project, the energy conversion efficiency of the impact runner independently developed by Harbin Electric Group has reached the world advanced level. The runner adopts forging welding structure, consisting of 1 wheel hub forging and 21 bucket forgings, with a welded weight of 90.8 tons.
Impingement turbine is a hydraulic machine which uses pressure pipe to guide water flow and impingement runner for energy conversion. The design head of Zhala power Station is 671 meters, and the runner is one of the most important force and flow components that directly affect the efficiency of the unit. In the operation state of the unit, it is always subjected to a high frequency of dynamic pressure, which plays a crucial role in the stable operation and safety of the unit, and the welding manufacturing requirements are extremely strict.
As the world’s largest single capacity impact unit runner, its hub forging diameter of 4.7 meters, thickness of 1 meter, set a martensitic stainless steel largest forging world record; After processing, the maximum outside diameter of the runner is 6.23 meters and the maximum width is 1.34 meters, which is also the largest impact runner in the world. And due to material, shape, size and other reasons, welding, processing and other links of the manufacturing technology, are in the forefront of related fields, explore the manufacturing process, there are many risk factors and uncertainties, welding manufacturing requirements are extremely high, extremely difficult. In order to break through the welding difficulties of Zara 500 MW impact runner, Harbin Electric Motor Company has carried out technical research, adopted digital simulation technology, carried out research on die forging technology of large water bucket, and selected the “forging welding” manufacturing process route with excellent performance and efficiency; Through three-dimensional testing simulation calculation, the optimal welding parameters were explored and selected. The wheel hub and bucket made of martensitic stainless steel were welded together with high strength and toughness weld, which improved the impact toughness and fatigue resistance of the runner.
Through the welding and manufacturing of the Zara 500 MW impact unit wheel, the electric motor company of Harbin Electric Group has cracked the welding problems of ultra-large ultra-thick low-carbon martensitic stainless steel forgages, overcome the difficulties of high-efficiency and high-strength welding manufacturing of complex curved ultra-thick water bucket, mastered the key technology of ultra-high bonding strength surface strengthening manufacturing process, and promoted the major breakthrough in China’s electric power equipment manufacturing technology.It has set a new milestone in the process of high-quality development of China’s energy equipment manufacturing industry.
Titanium Alloy Adoption in Aerospace Expands to Enhance Fuel Efficiency and Aircraft Longevity
The aerospace industry continues to prioritize the use of advanced, lightweight materials to meet growing demands for fuel efficiency and longer operational lifespans. One of the key materials driving this evolution is titanium alloy, which is increasingly being utilized in the production of aircraft components. In a recent announcement, a leading international airline revealed that its new generation of aircraft will feature even more titanium alloy parts, optimizing performance, reducing fuel consumption, and extending the aircraft’s operational life.
Titanium Alloys Gain Ground in Aerospace Applications
Titanium alloys have long been favored in aerospace manufacturing due to their unique properties—low density, high strength, corrosion resistance, and excellent performance in extreme temperatures. These characteristics make titanium alloys ideal for critical aircraft components, including the fuselage frame, engine parts, and landing gear.
As aircraft manufacturers continue to push the boundaries of innovation, titanium alloys are being used in an increasing number of high-stress areas, where both weight and strength are of paramount importance. This expansion of titanium alloy applications is driven by the need for more fuel-efficient, environmentally-friendly, and durable aircraft.
Fuel Efficiency and Aircraft Longevity Benefits
The adoption of titanium alloys in aircraft design delivers several key benefits. One of the most significant advantages is the reduction in the overall weight of the aircraft, which directly translates into improved fuel efficiency. Lighter aircraft require less power to achieve and maintain flight, resulting in lower fuel consumption. This not only helps airlines reduce operational costs but also contributes to decreasing greenhouse gas emissions.
Additionally, titanium alloys’ exceptional resistance to corrosion and high-temperature performance extends the lifespan of critical components. Aircraft using titanium parts require less frequent maintenance and have reduced parts replacement costs over the long term, offering airlines a cost-effective solution that improves both operational efficiency and asset longevity.
Expanding Applications of Titanium Alloys in the Mechanical Industry
The aerospace industry’s increased use of titanium alloys has also led to broader applications of the material across other sectors. As manufacturing processes evolve and the cost of production decreases, titanium alloys are finding their way into automotive, marine, energy, and other high-performance industries.
In particular, industries requiring parts that can withstand extreme conditions—such as high stress, high temperatures, and corrosive environments—are increasingly turning to titanium alloys for their exceptional mechanical properties. As titanium alloy technology continues to advance, more industries are expected to adopt the material, further expanding its use across a variety of mechanical manufacturing applications.
The Future of Titanium Alloys in Aerospace and Beyond
The future of titanium alloys in aerospace is bright, with ongoing research and development aimed at enhancing their performance and reducing production costs. As titanium alloy production processes improve and economies of scale are realized, the material’s widespread adoption is expected to grow in both aerospace and other industries.
The continued expansion of titanium alloy use reflects broader trends in the aerospace sector, which is increasingly focused on sustainability, cost reduction, and high-performance standards. With their unique properties and numerous advantages, titanium alloys are poised to play a pivotal role in shaping the future of the aerospace industry and beyond.
The Influence of Heat Treatment Process of Molds on The Economy of Forgings
Heat treatment is one of the indispensable and important processes in the manufacturing process of forging molds, which plays a crucial role in the lifespan of the molds. According to the requirements of specific forging processes, targeted heat treatment processes are developed to match the strength (hardness) and toughness of the mold appropriately, ensure reasonable and uniform hardness on the surface of the mold body and cavity, achieve fine and uniform grain size, prevent oxidation and decarburization, reduce residual stress and deformation, and improve the life and stability of the mold. The adoption of new heat treatment processes can tap into the potential of materials and significantly improve the lifespan of molds at a small cost. For example, low temperature quenching is used for high carbon cold forging dies to obtain more Flat noodles martensite, which can improve toughness, reduce die deformation and quenching cracks, and thus improve die life; Vacuum heat treatment has the advantages of no oxidation, decarburization, degassing, uniform heating, and small deformation, which is also beneficial for improving the service life of molds.
The effect of surface treatment on strengthening the surface of the mold cavity and improving the mold life is not only significant, but also cost-effective. It is a twice the result with half the effort strengthening mold process method and the preferred process for improving mold economy. The surface treatment methods for mold cavity strengthening that have been applied and have application potential include surface deformation (shot peening, extrusion, rolling, etc.) strengthening, surface phase transformation strengthening, surface diffusion strengthening, implantation strengthening and other surface modification technologies, thin film technologies such as physical vapor deposition and chemical vapor deposition, as well as coating technologies such as electrochemical deposition (electroplating) and thermal spraying. The characteristics and application status of these processes will also be discussed in subsequent chapters of this book.
What Is A Hinge Forging?
Hinge shaft forging is a kind of mechanical parts made by forging process, mainly used to connect and support rotating parts, common in various mechanical equipment hinged parts. Its material is usually made of high-strength steel, such as alloy structural steel, carbon structural steel, etc., to ensure that it has good mechanical properties and wear resistance. The forging process can make the internal structure of the material more dense, improve the strength and durability of the hinge shaft forging.
In addition, according to the specific application scenario and working conditions, hinge shaft forgings may also choose stainless steel, copper alloy, aluminum alloy and other materials for forging. Stainless steel has good corrosion resistance and oxidation resistance, suitable for hinge shaft forgings that need to be exposed to moisture or corrosive environment for a long time; Copper alloys and aluminum alloys have light weight and good thermal conductivity, and are suitable for occasions where weight and heat dissipation need to be reduced.
In the forging process, the raw material goes through process steps such as heating, deformation and cooling to form a hinge shaft forging with the desired shape and size. Forging can not only improve the strength and hardness of the material, but also improve its organization and performance, so that the hinge shaft forging has better wear resistance, impact resistance and fatigue resistance.
Hinge shaft forgings are widely used in various mechanical equipment, such as automobiles, ships, aerospace, engineering machinery and other fields. They play an important role in connecting, supporting and transmitting torque, and are one of the key parts to ensure the normal operation of mechanical equipment and extend the service life.
In order to meet the needs of different fields and working conditions, the design and production of hinge forgings usually need to follow strict standards and specifications. This includes specific requirements for its size, shape, material properties, surface quality and so on. The manufacturer needs to customize the production according to the drawings or technical requirements provided by the customer to ensure that the quality of the hinge shaft forging meets the relevant standards and customer requirements.
In terms of quality control, hinge shaft forgings need to undergo strict inspection and testing. This includes the testing of its dimensional accuracy, material composition, mechanical properties, surface defects, etc., to ensure that its quality meets relevant standards and regulations. In addition, the forging process needs to be monitored and controlled to ensure the stability and reliability of the production process.
With the continuous development of the manufacturing industry and the continuous progress of technology, the production process and material selection of hinge forgings are also constantly innovative and improved. For example, the use of advanced forging technology and equipment can improve production efficiency and product quality; The development of new materials can improve the mechanical properties and corrosion resistance of hinge shaft forgings. The application of intelligent and automatic technology can realize the automation and intelligent control of the production process, improve production efficiency and reduce costs.
In short, hinge shaft forging as an important part of mechanical equipment, its quality and performance have an important impact on the normal operation and service life of the equipment. Therefore, in the design and production process, it is necessary to fully consider its application scenarios and working conditions, select the appropriate materials and processes, and ensure that its quality meets the relevant standards and customer requirements.
What are the applications of track walking wheel forgings?
Core Tip: The application of track walking wheel forgings is quite extensive, mainly used for various equipment that needs to move along tracks or fixed paths. The following are its main application areas:
In addition, rail car wheel forgings are widely used in industrial automation, material handling, and other fields, providing stable and reliable support for various equipment that needs to move along fixed paths.
Please note that these are only some of the main application areas of track walking wheel forgings. With the advancement of technology and the expansion of application fields, their application scope will continue to expand.